End to End Supply Chain Management Process
The supply chain management process covers supply chain planning, procurement/supplier management, manufacturing, inventory/warehouse management, shipping/delivery, and return.
Supply Chain Planning
Supply chain planning involves the process of coordinating and managing the flow of goods, services, and information from the raw materials stage to the end customer. There are several key aspects of planning that are involved in supply chain management, including:
- Demand forecasting: Demand forecasting involves predicting future demand for goods and services. This is an important aspect of supply chain planning as it helps companies ensure that they have the right amount of inventory on hand to meet customer demand.
- Capacity planning: Capacity planning involves determining the amount of production capacity that is needed to meet demand. This includes determining the number of units that can be produced, as well as the amount of raw materials and other resources that are required.
- Inventory management: Inventory management involves planning and coordinating the flow of inventory through the supply chain. This includes determining the right level of inventory to maintain, as well as managing the movement and storage of inventory.
- Sourcing and procurement: Sourcing and procurement involves identifying and managing the flow of goods and services from suppliers. This includes identifying and evaluating potential suppliers, negotiating terms and conditions, and managing the purchasing process.
- Transportation and logistics: Transportation and logistics involve coordinating the movement of goods and materials from one location to another. This includes determining the most efficient and cost-effective modes of transportation, as well as managing the loading and unloading of goods.
Overall, supply chain planning involves coordinating and managing a wide range of activities to ensure that goods and materials are delivered to the end customer in a timely and cost-effective manner.
- What is Supply Chain Planning and Strategy? – Refreshes Constantly.
- Further information and training on supply chain planning.
Procurement
Procurement is the process of purchasing goods and services from suppliers and is a critical part of supply chain management. There are several key aspects of procurement that are involved in supply chain management, including:
- Supplier selection: Supplier selection involves identifying and evaluating potential suppliers in order to choose the most suitable ones for a company’s needs. This may involve considering factors such as cost, quality, delivery schedules, and the supplier’s reputation.
- Negotiation: Negotiation involves the process of establishing the terms and conditions of a procurement agreement, including the price, delivery schedules, and payment terms. This may involve negotiating with suppliers to secure the best possible terms for the company.
- Order placement: Order placement involves issuing a purchase order to a supplier and specifying the goods or services that are being purchased. This may include providing detailed specifications and delivery schedules.
- Receiving and inspection: Receiving and inspection involves receiving the goods or services that have been purchased and verifying that they meet the company’s quality and quantity requirements. This may include conducting inspections to ensure that the goods or services meet the specified standards.
- Payment: Payment involves settling the financial obligations associated with a procurement agreement, including paying the supplier for the goods or services that have been received.
Overall, procurement is a critical aspect of supply chain management that involves coordinating and managing the purchasing of goods and services from suppliers.
- What is Supplier Management and Procurement? – Refreshes Constantly.
- Further information and training on procurement.
What is Procurement? | Procurement Process.
Tips to Negotiate Lower Real Estate Commission.
NAR Settlement Real Estate Changes.
Manufacturing
Manufacturing is the process of transforming raw materials into finished goods, and it is a critical part of the supply chain. There are several key aspects of manufacturing that are involved in supply chain management, including:
- Production planning: Production planning involves determining the most efficient and cost-effective way to produce goods. This includes identifying the production processes and resources that are needed, as well as determining the production schedule and quantities.
- Production management: Production management involves coordinating and overseeing the production process to ensure that it is running smoothly and efficiently. This may include managing the flow of materials, monitoring production equipment, and ensuring that production meets quality standards.
- Quality control: Quality control involves ensuring that finished goods meet the specified quality standards. This may involve implementing quality control measures such as inspections and testing to ensure that the goods meet the required specifications.
- Inventory management: Inventory management involves coordinating the flow of inventory through the production process. This includes determining the right level of inventory to maintain, as well as managing the movement and storage of inventory.
- Distribution: Distribution involves getting finished goods to the end customer. This may involve using various distribution channels, such as retail stores, e-commerce platforms, or wholesalers.
Overall, manufacturing is a critical part of the supply chain that involves transforming raw materials into finished goods and ensuring that they meet the required quality standards before being distributed to the end customer.
- What is Manufacturing? – Refreshes Constantly.
- Further information and training on manufacturing.
- What is Industry 4.0?
High-tech Production Without People | Industry 4.0Â
Dark Factory – Automated Factory with Minimal Human Involvement.
Boeing Quality Control Process for 737 Max Planes.Â
Inventory and Warehouse Management
Inventory and warehouse management are critical aspects of supply chain management that involve coordinating the flow of goods and materials through the supply chain. Some key aspects of inventory and warehouse management include:
- Inventory planning: Inventory planning involves determining the right level of inventory to maintain in order to meet customer demand while minimizing costs. This may involve considering factors such as lead times, demand patterns, and safety stock levels.
- Inventory control: Inventory control involves managing the flow of inventory through the supply chain. This includes activities such as receiving, storing, and distributing goods, as well as monitoring inventory levels and ensuring that they are accurate.
- Warehouse design and layout: Warehouse design and layout involves determining the most efficient and cost-effective way to organize and store inventory in a warehouse. This may include considering factors such as the type of goods being stored, the equipment and resources that are needed, and the flow of goods through the warehouse.
- Material handling: Material handling involves the movement and storage of goods within a warehouse. This may include the use of equipment such as forklifts and conveyor belts to move and store goods, as well as manual handling techniques.
- Order fulfillment: Order fulfillment involves processing and completing orders for customers. This may include activities such as picking and packing orders, as well as managing the shipping and delivery process.
Overall, inventory and warehouse management are critical aspects of supply chain management that involve coordinating the flow of goods and materials through the supply chain.
- What is Distribution, Warehouse and Inventory Management? – Refreshes Constantly.
- Further information and training on distribution and warehousing.
Transportation, Shipping and delivery.
Shipping and delivery are critical aspects of supply chain management that involve coordinating the movement of goods and materials from one location to another. Some key aspects of shipping and delivery include:
- Transportation planning: Transportation planning involves determining the most efficient and cost-effective way to transport goods and materials. This may include considering factors such as the type of goods being transported, the distance they need to travel, and the available modes of transportation.
- Route optimization: Route optimization involves determining the most efficient route for transporting goods and materials. This may involve considering factors such as distance, traffic, and delivery schedules.
- Freight management: Freight management involves coordinating the movement of goods and materials by air, land, or sea. This may include managing the loading and unloading of goods, as well as tracking the movement of goods in real-time.
- Distribution: Distribution involves getting goods and materials to the end customer. This may involve using various distribution channels, such as retail stores, e-commerce platforms, or wholesalers.
- Customer service: Customer service involves providing assistance and support to customers during the delivery process. This may include activities such as tracking orders, providing updates on delivery schedules, and handling any issues or concerns that may arise.
Overall, shipping and delivery are critical aspects of supply chain management that involve coordinating the movement of goods and materials from one location to another and ensuring that they are delivered to the end customer in a timely and cost-effective manner.
- What is Transportation, Logistics and Shipping? – Refreshes Constantly.
- Further information and training on shipping and transport.
Supply Chain Disruption Scenario: Cyberattack on US Port Infrastructure.
Automated Truck Loading and Unloading System | Q-Loader.
How Shipping Containers Control Global Trade.
Return
Returns are a common part of the supply chain process, and there are several key aspects of managing returns that are involved in supply chain management. These include:
- Return policy: A return policy is a set of guidelines that outlines the terms and conditions under which a customer can return a product. This may include information such as the time frame in which a return can be made, the types of products that are eligible for return, and the process for obtaining a refund or replacement.
- Return handling: Return handling involves managing the process of receiving and processing returned products. This may include activities such as inspecting the returned product, determining whether it is eligible for a refund or replacement, and issuing a refund or processing a replacement.
- Reverse logistics: Reverse logistics involves coordinating the movement of returned products from the customer back to the company or a third-party provider. This may involve using various transportation modes and coordinating the handling and storage of the returned product.
- Refunds and credits: Refunds and credits involve issuing a refund or credit to the customer for the returned product. This may involve processing the refund or credit through the company’s payment system or issuing a physical check or credit card credit.
- Product disposal: Product disposal involves disposing of returned products that are no longer suitable for sale or that cannot be resold. This may include activities such as recycling or donating the product, or disposing of it in an environmentally responsible manner.
Overall, managing returns is a critical aspect of supply chain management that involves coordinating the movement of returned products and ensuring that they are handled in a timely and cost-effective manner.
What is Return and Reverse Logistics? – Refreshes Constantly.
Supply Chain Operations Reference Model or SCOR – Meaning, Definition, Process and Example
‘Re-imagining’ the End-to-End Supply Chain
End to End Supply Chain.
An end-to-end supply chain is a system that encompasses all the activities involved in getting a product or service from the supplier to the customer. It includes the following stages:
- Planning: This stage involves determining the demand for the product or service, as well as the supply chain resources that will be needed to meet that demand.
- Procurement: This stage involves acquiring the raw materials or components needed to produce the product or service.
- Manufacturing: This stage involves transforming the raw materials or components into the finished product or service.
- Warehousing: This stage involves storing the finished product or service until it is needed.
- Distribution: This stage involves transporting the finished product or service to the customer.
- Customer service: This stage involves providing support to customers after they have purchased the product or service.
The end-to-end supply chain is a complex system that involves many different players, including suppliers, manufacturers, distributors, retailers, and customers. It is important to manage the end-to-end supply chain effectively in order to ensure that products or services are delivered to customers in a timely, efficient, and cost-effective manner.
Here are some of the benefits of an end-to-end supply chain:
- Improved visibility: An end-to-end supply chain provides visibility into all the activities involved in getting a product or service to the customer. This can help to identify and address inefficiencies and bottlenecks.
- Reduced costs: An end-to-end supply chain can help to reduce costs by optimizing the flow of goods and materials.
- Improved customer service: An end-to-end supply chain can help to improve customer service by providing visibility into the status of orders and deliveries.
- Increased flexibility: An end-to-end supply chain can help to increase flexibility by allowing for changes in demand or supply.
- Sustainability: An end-to-end supply chain can help to improve sustainability by reducing waste and emissions.
Overall, an end-to-end supply chain is a valuable tool for businesses that want to improve their efficiency, profitability, and sustainability.
Train by Primary SCM Process
- Plan it: What is Supply Chain Planning and Strategy?
- Buy it: What is Supplier Management and Procurement?
- Store it: What is Distribution, Warehouse and Inventory Management?
- Make it: What is Manufacturing?
- Ship it: What is Transportation, Logistics and Shipping?
- Return it: What is Return and Reverse Logistics?
Explore SCM Processes. What is…
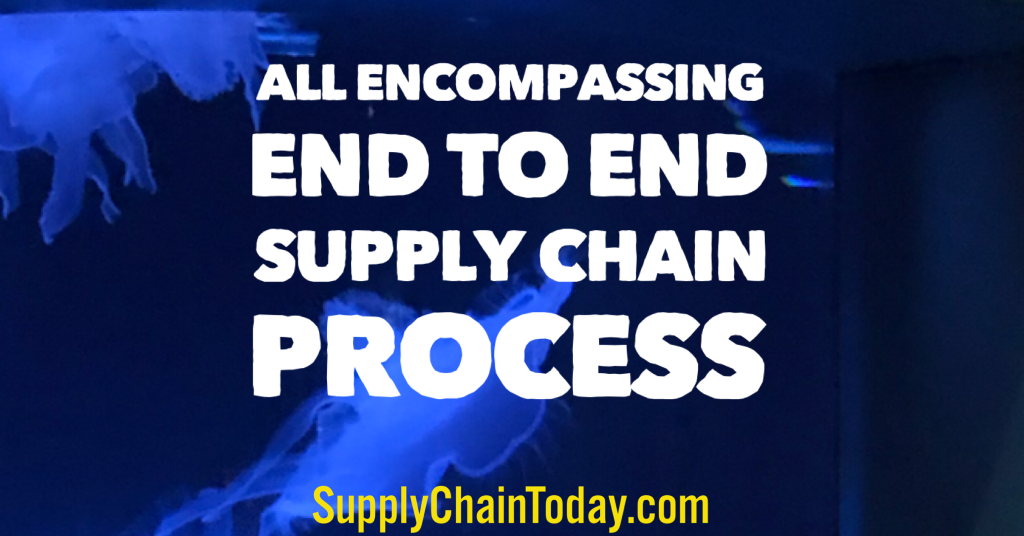